Wie Unternehmen durch optische Kommunikation die Effizienz in der Produktion erhöhen können.
Im Zentrum der Methoden der Lean Production steht die kontinuierliche Verbesserung. Damit ist unter anderem die Vermeidung von Verschwendung (wie überflüssigen Lagerbeständen oder nicht-ergonomischen Bewegungen) fest verbunden. Doch wie soll man reagieren, wenn konkrete Störungen auftreten? Hier kommt in der Lean Production das visuelle Management ins Spiel: Dabei geht es darum, Informationen visuell so zu kommunizieren, dass jeder Mitarbeiter direkt erkennen kann, ob ein Prozess wie geplant verläuft oder ob Störungen auftreten – auch wenn er mit dem jeweiligen Prozess gar nicht vertraut ist. Dabei macht sich das visuelle Management die konkurrenzlose Kraft der Visualisierung zunutze. Die Informationsaufnahme des Menschen verläuft in der Regel folgendermaßen: Zu 83 % über das Auge, zu 11 % über das Ohr, zu 3,5 % über den Geruchssinn, zu 1,5 % über den Tastsinn und zu 1 % über den Geschmackssinn. Im ersten Beitrag unserer zweiteiligen Reihe über visuelles Management widmen wir uns visuellen Kontrollen und Andon-Systemen.
Die Welt der Lean Production
Weniger Verschwendung und mehr Wertschöpfung: Mit den Methoden der Lean Production machen Sie Ihre Fertigung gezielt effizienter. Im Whitepaper finden Sie eine kompakte Einführung.
JETZT SICHERN
Die Rolle von visuellen Kontrollen
Unter visuellen Kontrollen versteht man eine Vorrichtung oder ein Symbol, das eine Information effektiv und unter Verwendung von möglichst wenigen oder keinen Worten am Ort des Geschehens platziert. Zu den visuellen Kontrollen zählen beispielsweise:
- Im Alltag: Ampeln, Straßenmarkierungen und Verkehrsschilder.
- Shadowboards: Es ist sofort erkennbar, wo welches Werkzeug hingehört und ob eines fehlt.
- Übereinstimmungen in Form und Farbe bei Stecker und Steckdosen: So gibt es keine Missverständnisse darüber, was wo hingehört.
- Farblich markierte Verkehrswege: Hierdurch werden die Wege von Personen und Fahrzeugen vorgeschrieben, um Unfälle zu vermeiden.
Zunächst gilt es eine Umgebung zu schaffen, in der nichtnormale Zustände von normalen Zuständen (also Standards) deutlich zu unterscheiden sind. Mit der bloßen Einführung von visuellen Kontrollen ist es jedoch nicht getan. Darüber hinaus muss eine entsprechende Kultur auf Basis des visuellen Managements im Unternehmen vorhanden sein. Dafür müssen die Arbeiter dahin entwickelt werden, dass sie das Richtige tun, wenn sie nichtnormale Zustände erkennen. Genauer gesagt: Es gilt sie zu ermächtigen, die richtigen Dinge tun zu dürfen. Wie das geht, schauen wir uns jetzt im Detail an.
Visuelles Management im Lean-Kontext: Andon
Zu den bekanntesten Fällen von visuellem Management im Kontext der Lean Production zählt das Andon Board. Andon bedeutet übersetzt „Laterne“. Ursprünglich wurden nur die traditionellen japanischen Laternen so genannt. Dann ging man dazu über, kleine Leuchten an Maschinen ebenfalls so zu bezeichnen. In diesem Kontext ist auch die Andon-Leine zu sehen. Dabei kann es sich tatsächlich um eine Leine oder auch um einen Knopf handeln. Der Mitarbeiter zieht bei einem Problem an der Leine, um zu signalisieren, dass etwas nicht stimmt. Über das Andon Board sieht ein Verantwortlicher, etwa der Teamleiter, zum einen, dass ein Problem da ist und zum anderen, wer Unterstützung anfordert. Wenn dieses nicht innerhalb der Taktzeit behoben werden kann, wird der Prozess in der Regel durch den Teamleiter gestoppt, um das Problem gründlicher untersuchen zu können.
Auf einem Andon-Board finden sich nicht nur Informationen zum Status einer Maschine, sondern auch zum Stand der Fertigung als solcher.
Auf diese Weise wird jedoch nicht nur der Vorgang unterbrochen – durch das Signal auf dem über dem entsprechenden Bereich angebrachten Andon Board ist zudem für alle Mitarbeiter direkt erkennbar, wo genau das Problem aufgetreten ist. Darüber hinaus gibt es auch Andon-Lichter, die an Maschinen angebracht sind und ähnlich wie Ampeln funktionieren. Auch hier steht jede Farbe für einen anderen Status (grün = Normalzustand, gelb = Wartung ist geplant, rot = Problem ist aufgetreten/Maschine wurde angehalten). Auf einem Andon-Board finden sich nicht nur Informationen zum Status einer Maschine, sondern auch zum Stand der Fertigung als solcher: Ist- und Sollzustand werden gegenübergestellt und visualisiert. Somit fungiert das Andon Board sowohl als Schrittmacher für die Produktion als auch als Mittel zur Motivierung der Mitarbeiter.
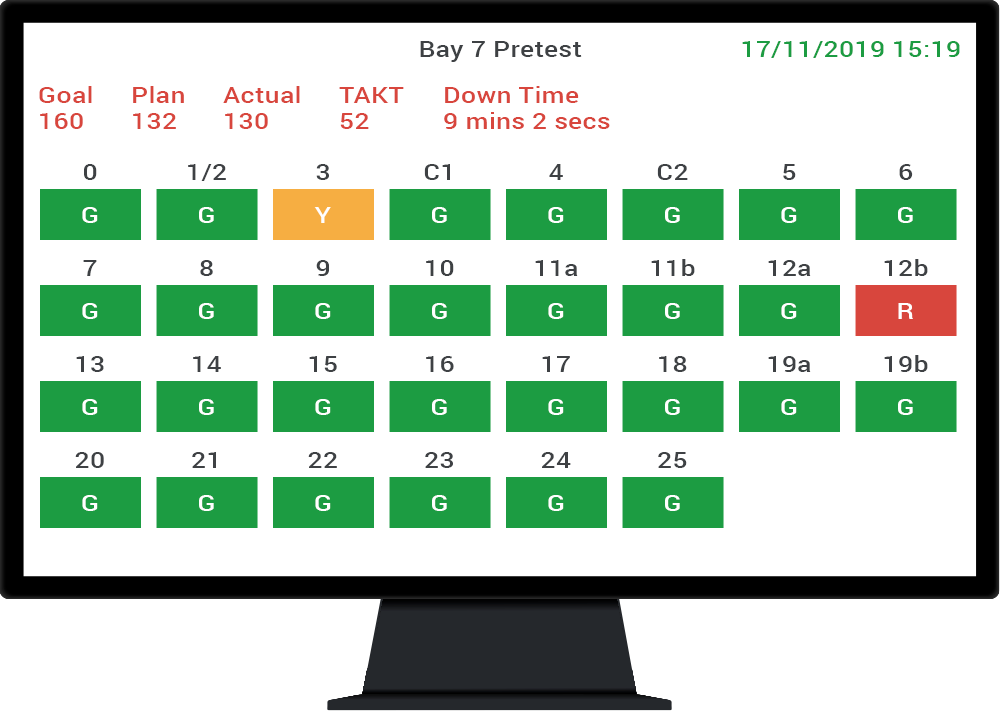
Der Prozess der Optimierung endet nie
Anhand eines Beispiels lässt sich die Effektivität des Einsatzes der Andon-Leine und des Andon Boards verdeutlichen: Im Toyota-Werk Nummi in den USA waren die Mitarbeiter angehalten, bei jedem Fehler an der Andon-Leine zu ziehen. Als Folge wurde dieser Fehler von den Teammitgliedern analysiert und zusammen behoben, eingeleitet von Applaus. Dies ist Ausdruck der für die Lean Production typischen, positiven Fehlerkultur, in der Fehler als Chance zur Verbesserung gesehen werden. Das Ergebnis der Maßnahmen: Im Zeitraum von nur drei Jahren konnte man die Anzahl der Züge an der Andon-Leine pro Schicht von 1000 auf 300 reduzieren. Damit ist diese Geschichte jedoch noch nicht zu Ende. Denn es handelt sich nicht um ein Ergebnis, mit dem sich Toyota zufriedengibt.
Was macht Toyota, wenn ein Prozess stabil läuft? Er wird verbessert.
Die geringere Anzahl der Andon-Züge macht deutlich, dass der Prozess jetzt stabiler läuft. Und was macht Toyota, wenn ein Prozess stabil läuft? Er wird verbessert. Deswegen ist es ein bewährter Schritt bei Toyota, Bestände aus dem Prozess zu nehmen und somit den Prozess zu verschlanken bzw. zu verbessern: Indem die Puffer verkleinert werden, ergeben sich unter Umständen für die Mitarbeiter wieder mehr Probleme. Dies führt wiederum zu mehr Andon-Zügen. Mit anderen Worten: Es herrscht nie Stillstand. Deswegen lautet die (nur scheinbar widersprüchliche) Ansage des Werkleiters an den Produktionsleiter: „Sorgen Sie dafür, dass wir wieder 1000 Andon-Züge pro Schicht haben.“ Hier wird besonders deutlich, wie entscheidend die kontinuierliche Verbesserung für die Lean-Philosophie ist.